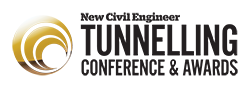
Entry deadline extended to 1 August
New Civil Engineer Tunnelling Conference & Awards brings together the entire tunnelling community for an interactive and immersive day filled with case studies, debate, future project updates and the Tunnelling Awards.
By joining us you can make new connections with project leads, gain insight into design and delivery innovations and understand the scope of future opportunities across sector. Whether you are designing a challenging shaft, delivering a complex transport tunnel or seeking to raise the profile of your solutions, this conference and awards is a great place to network and learn.
The 2025 Conference & Awards is on the 4 December in London and the award winners will be announced at a gala ceremony that evening.
New entry deadline: Friday 1 August 2025
NCE Tunnelling Festival in numbers